Digital Utilities
Digital Twin & AI Platform for Integrated Performance Management of Utilities
INNOVATION
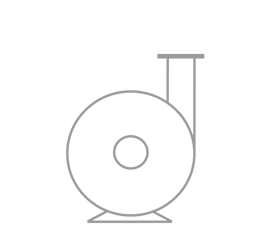
Virtual Pump Station
(Patent No 236496)
from Energy
Virtual Pump Station
INNOVATION
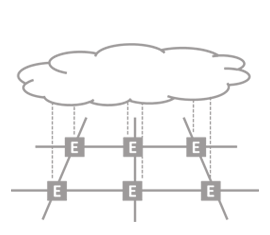
Water-Energy Grid
through energy
Smart Water-Energy Grid
INNOVATION
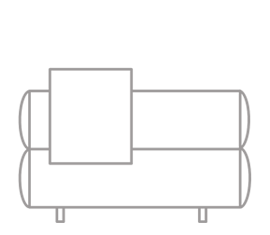
Plant Virtualization
(Patent Pending)
energy and temperature
Virtual Chiller Plant
INNOVATION
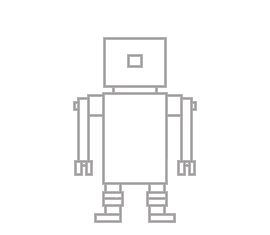
Sustainability Cyborg
Sustainability Cyborg
How it Works?
Virtual Metering
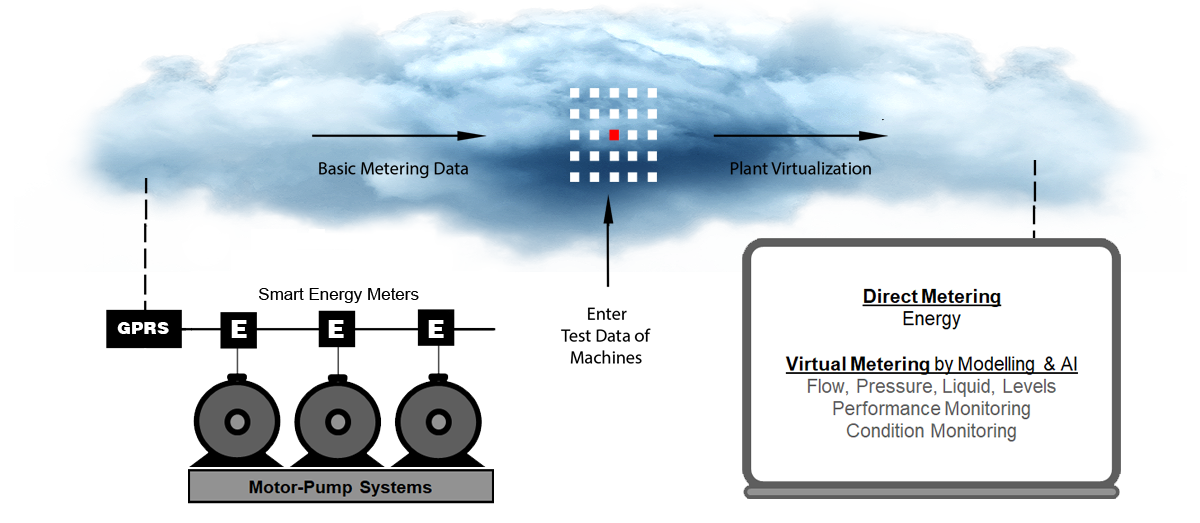
Steps to Engage Datamatrix
1
- Provide name plate data and site test/audit data of critical machines
2
- Establish energy data communication of critical machines.
3
- Establish header temperature data communication (for HVAC)
4
- Remote monitoring analytics and automation through Datamatrix Cloud
Compare Technologies
Features | Conventional methods | Datamatrix approach |
TECHNOLOGY |
Limited Intelligence, require System Engineering & Integration Each parameter is independently metered and integrated |
Use Digital Twins & Artificial Intelligence (AI), remotely configured based on test data Dynamic model computes all parameters form energy signature validate them using basic metering |
METERING |
Requires dedicated costly meters and detailed instrumentation Require dedicated meter for each fluid parameter, Flow, Pressure |
Fluid Parameters computed from by Virtual Meter (Datamatrix Patent) Require only low-cost meters (energy meters and temperature sensors) |
PERFORMANCE MONITORING |
Monitor only System & Process Performance Each parameter is independently metered and integrated |
Monitor Equipment, System & Process Performance of all equipment Dynamic model compute all parameters and validate them using basic metering |
CONDITION MONITORING |
Condition monitoring requires separate sets of Instrumentation Relationship between parameters is not established for optimization |
Condition monitoring using basic metering with performance modelling Establish complex interrelationship (Fluid | Water | Energy | Asset nexus) |
ASSET MANAGEMENT |
Only energy consumption and system performance is monitored Predictive Maintenance is Not Possible, without separate system |
Tracks Energy consumption, energy loss & Life Cycle Cost of equipment
Predictive Maintenance & Condition Based Maintenance |
BEST PRACTICES |
Standalone systems with limited options for third party collaboration
Best practices are to be followed as a separate assignment |
Cloud based collaborative multi partner working environment
Seamless Integration to Best Practices ISO 41001, 50001, 55000, 45000) |
MEASURMENT & VERIFICATION |
Performance Measurement & Verification is manually done
To be designed independently - prone to human error |
Performance Measurement & Verification is automated
Conforms to IPMVP and facilitate all IPMVP Options |
PROJECT COST |
CAPEX
Technology cost generally paid upfront |
OPEX - Technology Cost Recovered from Saving.
➢ Platform as a service (PaaS)
➢ Performance contract
|
IMPLEMENTATION |
Implementation must be done in one go
Generally Managed from one location mostly only monitoring |
Implementation is done progressively with tangible outcomes at each stage
Managed from multiple geographies with continuous commissioning - facilitates multiple advantages |
Services, Deliverables & Expected Outcomes
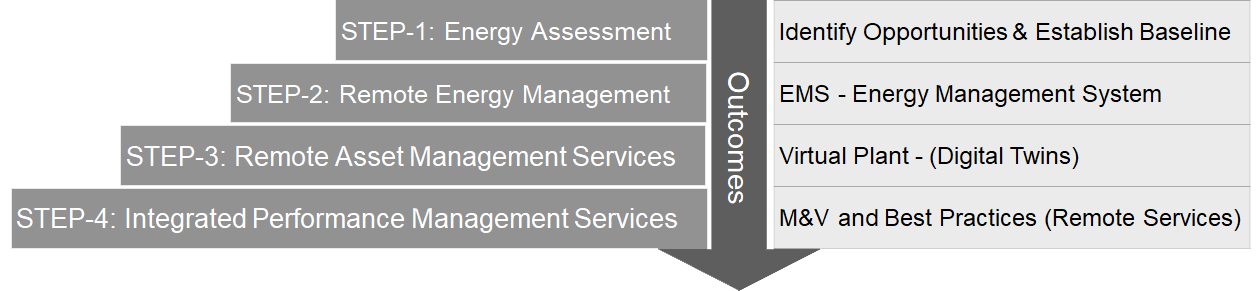
Tangible Benefits |
10% Energy Cost Reduction by Optimisation 10% Energy Cost Reduction by Asset Managment 20% Asset Life Enhancement |
Intangible Benefits |
Digital Twins of the Building / Plant Integrated Performance Management Remotely Managed Engineering Services Sustainable Facilities Management |
Used by industry leaders
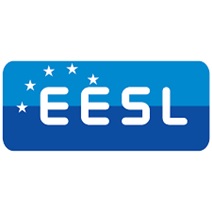
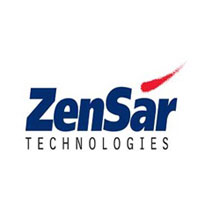
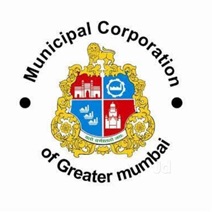
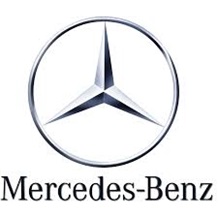
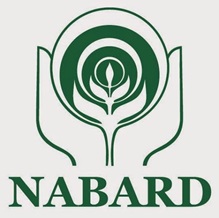
Recent awards
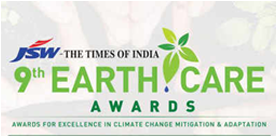
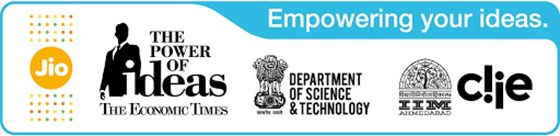
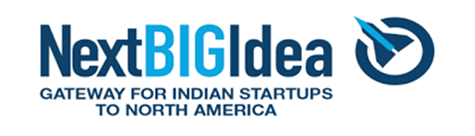